汽車發動機下護板是發動機內部結構的重要組成部分,主要負責保護發動機內部部件免受碰撞、沖擊和高溫的損害。隨著汽車制造技術的不斷進步,發動機下護板的材質選擇也在不斷演變,以滿足更高的安全性、耐用性和輕量化要求。本文將探討汽車發動機下護板的常見材質及其優缺點,幫助讀者更好地了解如何選擇適合的材料。
一、發動機下護板的功能與要求
發動機下護板主要承擔以下幾項功能:
1. 保護發動機內部部件:防止散熱器、氣缸蓋等部件因碰撞或沖擊而損壞。
2. 隔熱與保溫:隔絕高溫從發動機內部散布到其他部位,防止熱損害。
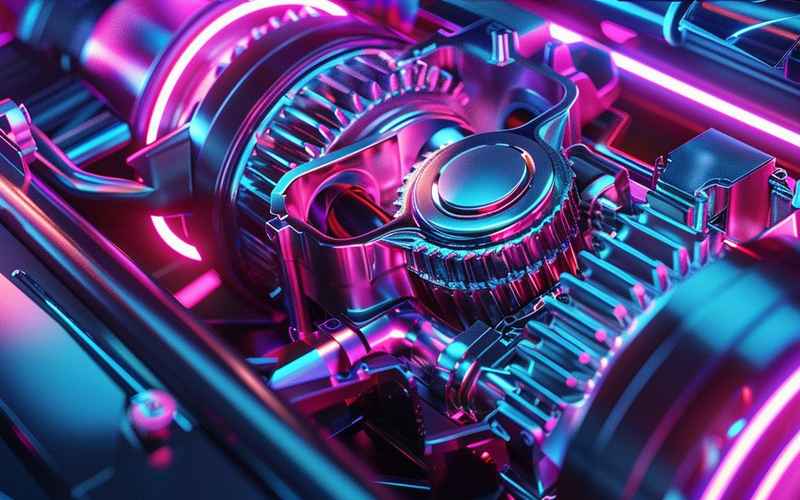
3. 抗沖擊:抵御發動機在運行過程中由于振動、顫動等原因造成的沖擊力。
4. 美觀與結構穩定性:為發動機提供整體結構的穩定性,同時在外觀上與車身風格協調。
由于發動機運行時溫度較高,且發動機部件在運行中會產生較大的振動和沖擊力,因此發動機下護板的材質需要具備以下特性:
高強度與高剛性:能夠承受高溫、高沖擊力的雙重考驗。
耐熱:能夠在高溫環境下保持穩定性能。
輕量化:降低整車重量,提高能效與駕駛性能。
抗腐蝕:防止在含有酸性、堿性或腐蝕性氣體的環境中發生化學反應。
成本效益:在滿足性能要求的前提下,具有較低的采購和生產成本。
二、常見發動機下護板材質及特點
1. 鋁合金
優點:
鋁合金的密度較低,輕量化性能優異,適合需要降低整車重量的車型。
具有較高的強度和剛性,能夠很好地承受高溫、高沖擊力的雙重壓力。
耐熱性能較好,能夠在較高溫度下保持穩定。
抗腐蝕性能良好,能夠抵御一般的環境腐蝕。
易于加工成形,且成本相對較低。
缺點:
與鋼材相比,鋁合金的成本較高,特別是在大批量生產時。
某些鋁合金材料在低溫環境下的性能可能不如鋼材。
2. 碳纖維/復合材料
優點:
強度高、剛性好,能夠承受極高的機械應力。
耐熱性能優于傳統鋁合金,適合高溫環境。
微型化設計可為發動機提供更好的空間適應性。
具有較高的輕量化比,能夠顯著降低發動機重量。
缺點:
成本較高,制作工藝復雜,初期投入較大。
復合材料的可加工性和耐腐蝕性能可能不如傳統材料。
應用實例:在一些高性能或高端車型中,碳纖維復合材料被廣泛應用于發動機下護板。
3. 鋼材
優點:
成本低廉,生產工藝簡單,易于大批量加工。
強度高,耐沖擊性能優異,能夠承受較大的機械應力。
耐熱性能較好,適用于中等溫度環境。
易于進行焊接、疊加等加工,適合復雜的結構設計。
缺點:
重量較大,降低了整車能效和駕駛性能。
耐熱性能有限,可能需要額外的冷卻措施。
抗腐蝕性能一般,容易在惡劣環境下發生腐蝕。
4. 塑料/高性能塑料
優點:
輕量化比高,能夠顯著降低發動機重量。
耐溫性能較好,能夠適應較高的工作溫度。
復合度高,可與其他材料形成結構復合,提升整體性能。
制作工藝多樣,加工成本相對較低。
缺點:
強度和剛性一般,可能不夠承受高沖擊力。
耐久性較差,容易在高溫、高磨損環境下損壞。
抗腐蝕性能有限,容易受到化學腐蝕的影響。
5. 鈦合金
優點:
密度低于鋼材,輕量化性能優異。
強度高,剛性好,能夠承受較大的機械應力。
耐熱性能較好,適合高溫環境。
抗腐蝕性能優于鋁合金,適合更多的應用場景。
缺點:
制作成本較高,且供應鏈相對緊張。
與鋁合金相比,鈦合金在熱處理和加工方面有一定的技術門檻。
三、選擇發動機下護板材質的關鍵標準
在選擇發動機下護板材質時,需要綜合考慮以下因素:
1. 車型需求:
高性能車型通常會選擇輕量化、高強度的材料,如碳纖維復合材料或鈦合金。
經濟型車輛則可能以鋼材或鋁合金為主,兼顧成本與性能。
2. 溫度環境:
高溫發動機通常需要耐熱材料,如鋁合金或碳纖維復合材料。
溫和或低溫發動機可選擇成本較低的鋼材或塑料。
3. 制造工藝:
復雜工藝如復合材料的制作需要較為先進的設備和技術支持。
簡單工藝如鋼材或塑料的制造成本較低,適合大批量生產。
4. 預算限制:
高端車型可能愿意為更好的材質支付更高費用。
中低端車型則更注重成本效益。
四、未來發展趨勢
隨著汽車制造工業的技術進步,發動機下護板的材質選擇將更加注重輕量化、高強度、耐熱與耐腐蝕性能。新興材料如高強度塑料、自我修復材料以及具有更高顆粒表面的鈦合金等將逐漸進入市場。環保因素也會對材料選擇產生深遠影響,如可回收、可降解的材料可能成為未來的熱點。
選擇發動機下護板的材質需要綜合考慮性能、成本、制造工藝以及應用場景等多個因素。隨著技術的不斷進步,未來的發動機下護板將更加智能化、環保化,為汽車性能提供更強的保障。